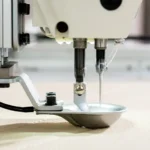
Ultrasonic Sewing: Fast, Seamless, and Eco-Friendly
October 5, 2024
What is a Tote Bag?
October 20, 2024Flexo printing, short for flexographic printing, is a modern printing technique that has revolutionized the packaging and labeling industries. Known for its versatility, efficiency, and ability to print on a wide range of substrates, flexo printing has become a preferred choice for many manufacturers. This article delves into the fundamentals of flexo printing, its history, advantages, applications, and future prospects in the printing industry.
Understanding Flexo Printing
Flexo printing is a rotary printing process that uses flexible relief plates to transfer ink onto various substrates. The process can print on a wide range of materials, including plastic, paper, cardboard, and even metallic surfaces. Unlike traditional printing methods that use rigid plates, flexographic plates are made from rubber or photopolymer, which allows for better adaptability and more intricate designs.
The Flexo Printing Process
The flexo printing process consists of several key stages:
- Plate Preparation: The first step in flexo printing involves creating the printing plates. These plates can be made from various materials, including rubber or photopolymer. The desired image or design is transferred to the plate using a laser engraving process or through a photographic method. The raised areas of the plate are what will come into contact with the substrate.
- Ink Application: Flexo printing uses fast-drying, low-viscosity inks. These inks are applied to the plate using an anilox roller, which meters the exact amount of ink needed for the printing process. The anilox roller has tiny cells that hold the ink, ensuring a consistent ink transfer.
- Printing: The substrate is fed through the press, where it comes into contact with the inked plate. The raised areas of the plate transfer the ink onto the substrate. This process can be performed in a single pass or multiple passes, depending on the complexity of the design and the number of colors involved.
- Drying: After the ink is applied, it must be dried quickly to prevent smudging or running. Flexo printing employs various drying techniques, including UV curing, hot air drying, and infrared drying, depending on the ink used and the substrate.
- Finishing: Once the ink has dried, the printed material may go through additional finishing processes, such as cutting, folding, or laminating, to create the final product.
History of Flexo Printing
Flexographic printing has its roots in the late 19th century when it was initially used for printing newspapers and packaging. The first flexo printing press was patented in 1890 by Charles and Albert K. B. Fehr, although the technology did not gain widespread acceptance until the 1920s.
In the early days, flexo printing relied on hard rubber plates and oil-based inks, which limited its capabilities. However, advancements in photopolymer technology in the 1970s significantly improved the quality and versatility of flexo printing. The introduction of water-based inks further enhanced the process by making it more environmentally friendly.
Today, flexo printing is a key player in the global printing industry, thanks to its ability to produce high-quality prints at high speeds and low costs.
Advantages of Flexo Printing
Flexo printing offers numerous benefits that make it an attractive option for manufacturers:
-
Versatility
One of the standout features of flexo printing is its versatility. It can print on various substrates, including plastic films, corrugated cardboard, paper, metal, and even textiles. This adaptability makes it suitable for numerous applications, from food packaging to industrial labels.
-
Speed and Efficiency
Flexo printing is known for its high-speed capabilities. The rotary nature of the press allows for continuous printing, which means large quantities of printed material can be produced in a short amount of time. This efficiency is particularly beneficial for large-scale production runs.
-
Cost-Effectiveness
Due to its speed and efficiency, flexo printing can be more cost-effective than other printing methods, especially for long runs. The low viscosity inks used in the process also reduce ink consumption, further driving down costs.
-
High-Quality Prints
Advancements in plate-making technology have allowed flexo printing to produce high-quality prints with sharp images and vibrant colors. The use of photopolymer plates also enhances the level of detail that can be achieved, making it suitable for complex designs.
-
Eco-Friendly Options
Flexo printing has embraced sustainability by utilizing water-based and UV-curable inks, which have lower environmental impacts compared to traditional oil-based inks. This shift toward eco-friendly practices aligns with the growing consumer demand for sustainable packaging solutions.
-
Low Maintenance
Flexo printing presses are generally easier to maintain than other types of printing equipment. The design of the presses allows for quick plate changes and minimal downtime, further enhancing productivity.
What is Flexo Printing?
Applications of Flexo Printing
Flexo printing finds applications across a diverse range of industries. Some of the most common uses include:
-
Packaging
Flexo printing is extensively used in the packaging industry for producing labels, bags, cartons, and wrappers. Its ability to print on various materials makes it ideal for food packaging, pharmaceuticals, cosmetics, and consumer goods.
-
Labels
Flexo printing is widely used for printing pressure-sensitive labels, shrink sleeves, and in-mold labels. Its capability to produce high-quality graphics makes it perfect for branding and marketing products.
-
Newspaper and Publication
While digital printing has gained popularity, flexo printing is still utilized for certain types of newspapers and publications, especially those requiring high-speed printing.
-
Flexible Packaging
The flexible packaging market has seen significant growth, and flexo printing plays a vital role in producing flexible films and pouches. Its ability to print on thin substrates allows for lightweight packaging solutions.
-
Textile Printing
Flexo printing is increasingly being adopted in the textile industry for printing patterns and designs on fabrics. The versatility of the inks allows for vibrant colors and intricate designs.
-
Stationery and Office Supplies
Flexo printing is also used in the production of stationery items, such as envelopes, business cards, and notepads, where high-quality prints are essential for branding.
Challenges of Flexo Printing
Despite its many advantages, flexo printing is not without its challenges. Some potential drawbacks include:
-
Initial Setup Costs
While flexo printing can be cost-effective for large runs, the initial setup costs for plates and presses can be high. This may deter smaller businesses from adopting the technology.
-
Limited Color Range
While flexo printing is capable of producing vibrant prints, it may not achieve the same color depth and detail as some other printing methods, such as offset printing. This limitation can be a concern for certain applications.
-
Sensitivity to Substrate Variability
Flexo printing can be sensitive to variations in substrate quality and thickness. Inconsistent materials may lead to issues with ink adhesion and print quality.
The Future of Flexo Printing
As technology continues to evolve, the future of flexo printing looks promising. Several trends and advancements are shaping the direction of the industry:
-
Digital Integration
The integration of digital technology with flexo printing is gaining traction. Hybrid printing solutions that combine digital and flexo capabilities allow for greater flexibility, customization, and shorter production runs, catering to the growing demand for personalized packaging.
-
Sustainability Initiatives
The push for eco-friendly practices is likely to continue influencing flexo printing. Manufacturers are increasingly seeking sustainable inks and substrates, leading to innovations in eco-friendly materials and processes.
-
Advanced Plate Technology
Ongoing advancements in plate-making technology are expected to enhance the quality and efficiency of flexo printing. The development of higher-resolution plates and faster production methods will enable printers to meet the demands of increasingly complex designs.
-
Market Growth
The global packaging industry is expected to continue growing, driven by rising consumer demand for packaged goods. As a result, the demand for flexo printing services will likely increase, presenting new opportunities for printers.
-
Automation
Automation in flexo printing presses will streamline production processes, reduce labor costs, and minimize errors. Fully automated systems will allow for faster changeovers and enhanced overall efficiency.
Conclusion
Flexo printing has established itself as a key player in the printing industry, offering a versatile and efficient solution for a wide range of applications. Its ability to produce high-quality prints on various substrates makes it an ideal choice for packaging, labels, and more. While there are challenges to address, the future of flexo printing looks bright, with advancements in technology, sustainability initiatives, and market growth paving the way for continued innovation. As the industry evolves, flexo printing is likely to remain at the forefront, adapting to the changing needs of manufacturers and consumers alike.