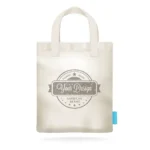
Custom Logo Printed Bags: Stylish and Practical Solutions
October 2, 2024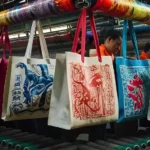
Unlock the Potential of Flexo Printing: The Ultimate Guide to Efficient and Versatile Printing
October 13, 2024In the realm of textile and garment manufacturing, innovation is key to staying competitive and meeting consumer demands. One such groundbreaking technology that has emerged in recent years is ultrasonic sewing. This method has transformed how fabrics are joined and has brought about significant advancements in speed, efficiency, and quality. This article explores the principles of ultrasonic sewing, its applications, benefits, and its future in the textile industry.
Understanding Ultrasonic Sewing
Ultrasonic sewing, also known as ultrasonic welding, is a process that uses high-frequency sound waves to bond materials together. Unlike traditional sewing, which relies on needles and thread, ultrasonic sewing utilizes ultrasonic vibrations to create heat through friction. This heat is sufficient to melt the edges of thermoplastic materials, allowing them to fuse without the need for additional adhesives or stitching.
You might also enjoy this article: Logo Printed PP Non-Woven Carry Bags for insights into sustainable and customizable bag options.
The Technology Behind Ultrasonic Sewing
Ultrasonic sewing machines typically consist of several key components:
- Ultrasonic Generator: This device converts electrical energy into high-frequency sound waves, usually in the range of 20 kHz to 40 kHz.
- Transducer: The transducer transforms electrical energy into mechanical vibrations. It is usually made from piezoelectric materials, which have the unique ability to convert electrical energy into mechanical motion.
- Sonotrode: This is a tool that amplifies the ultrasonic vibrations and directs them onto the material being welded. The sonotrode’s shape and design can vary depending on the application.
- Fixture or Anvil: This component holds the materials in place during the welding process. It ensures that the surfaces to be bonded are in proper alignment and can withstand the pressures of the ultrasonic vibrations.
The Process of Ultrasonic Sewing
The process begins when the operator places the materials to be joined onto the fixture. The ultrasonic generator emits high-frequency sound waves, which are transmitted through the transducer to the sonotrode. The sonotrode then applies these vibrations to the fabric edges, generating localized heat due to friction.
As the edges of the thermoplastic materials heat up, they soften and begin to melt. The sonotrode applies pressure to ensure the melted edges fuse together effectively. Once the ultrasonic vibrations stop, the material cools quickly, resulting in a strong, durable bond. This entire process typically takes only a few seconds, making ultrasonic sewing a highly efficient method for joining materials.
Applications of Ultrasonic Sewing
Ultrasonic sewing has found applications across various industries due to its versatility and efficiency. Here are some notable areas where this technology is making an impact:
- Apparel Manufacturing
In the fashion and apparel industry, ultrasonic sewing is used for joining lightweight fabrics, hems, and seams. The technique allows for a cleaner finish without visible stitching, which is often desirable in high-end garments. Additionally, ultrasonic sewing reduces the time required for assembly, enabling manufacturers to meet tight deadlines.
- Technical Textiles
Ultrasonic welding is widely utilized in the production of technical textiles, which are engineered for specific functions, such as protective clothing, medical textiles, and automotive interiors. For instance, in the medical field, ultrasonic sewing can create sterile, waterproof seams for surgical gowns and drapes, ensuring safety and compliance with health regulations.
- Home Textiles
Ultrasonic sewing is increasingly being used in the production of home textiles, including curtains, upholstery, and bedding. The ability to bond fabrics without stitching allows for more intricate designs and patterns, enhancing the aesthetic appeal of home furnishings.
- Non-Woven Fabrics
Non-woven materials, commonly used in hygiene products like diapers and feminine hygiene items, benefit significantly from ultrasonic sewing. The method allows for quick assembly while ensuring the integrity and performance of the non-woven layers.
- Packaging Industry
In the packaging sector, ultrasonic sewing is used to create bags and pouches from plastic or composite materials. This technique ensures strong seals that are resistant to leakage and contamination, making it suitable for food and medical packaging.
Benefits of Ultrasonic Sewing
Ultrasonic sewing offers a plethora of advantages that make it a compelling choice for manufacturers. Here are some key benefits:
- Speed and Efficiency
One of the most significant advantages of ultrasonic sewing is its speed. The process can bond materials in just a few seconds, drastically reducing production times compared to traditional sewing methods. This efficiency enables manufacturers to meet tight deadlines and respond quickly to market demands.
- Clean and Seamless Finish
Ultrasonic sewing produces a clean, seamless finish without visible stitches. This aesthetic appeal is particularly important in high-end fashion and technical textiles, where appearance and functionality are both critical.
- Reduced Labor Costs
Since ultrasonic sewing requires less manual intervention and can automate parts of the assembly process, labor costs are reduced. Fewer workers are needed on the production floor, allowing companies to allocate resources more effectively.
- Enhanced Durability
The bonds created through ultrasonic sewing are often stronger than traditional sewn seams. The process melts and fuses the materials, resulting in a joint that can withstand stress and strain better than conventional stitching.
- Environmentally Friendly
Ultrasonic sewing does not require adhesives, reducing the use of chemicals in the manufacturing process. This eco-friendly approach aligns with the growing trend toward sustainable practices in the textile industry.
- Versatility
Ultrasonic sewing can be applied to a wide range of materials, including various thermoplastics and textiles. This versatility allows manufacturers to explore new designs and applications, opening up opportunities for innovation.
Challenges of Ultrasonic Sewing
Despite its many advantages, ultrasonic sewing is not without challenges. Here are some potential drawbacks to consider:
- Material Limitations
Ultrasonic sewing is most effective with thermoplastic materials. Fabrics that do not have thermoplastic components may not bond well, limiting the scope of materials that can be used.
- Initial Investment
The initial cost of ultrasonic sewing equipment can be high, making it a significant investment for smaller manufacturers. However, the long-term savings in labor and time may offset these initial expenses.
- Training Requirements
Operators must be trained to use ultrasonic sewing machines effectively. The technology requires an understanding of the equipment and the materials involved, which may necessitate a learning curve for new users.
The Future of Ultrasonic Sewing
As the textile industry continues to evolve, ultrasonic sewing is poised for growth. The increasing demand for efficient, sustainable, and high-quality production methods will likely drive further innovation in this field. Here are some trends and predictions for the future:
- Integration with Automation
The integration of ultrasonic sewing with automated production lines is likely to become more prevalent. Robotic systems can work alongside ultrasonic sewing machines to enhance efficiency, reduce labor costs, and improve overall production rates.
- Development of New Materials
Research into new thermoplastic materials that can be effectively bonded through ultrasonic sewing may expand the technology’s applicability. Innovations in materials science could lead to new opportunities across various industries.
- Sustainability Focus
With increasing awareness of environmental issues, the demand for sustainable manufacturing processes will grow. Ultrasonic sewing, with its reduced reliance on chemicals and adhesives, aligns well with this trend. Manufacturers that adopt this technology may enhance their eco-friendly credentials, attracting more consumers.
- Customization and Design Flexibility
As consumers increasingly seek personalized products, the flexibility of ultrasonic sewing will be an asset. Its ability to create intricate designs without compromising structural integrity makes it ideal for custom apparel and textiles.
- Expansion into New Industries
Beyond textiles, ultrasonic sewing technology could find applications in other sectors, such as automotive, aerospace, and electronics. As industries look for innovative joining methods, ultrasonic welding could become a viable solution in various contexts.
What is Ultrasonic Sewing?
Ultrasonic sewing is revolutionizing the textile and garment manufacturing landscape by offering a fast, efficient, and environmentally friendly method for joining materials. With its ability to produce strong, seamless bonds in various applications, this technology is becoming increasingly important across industries. As manufacturers continue to seek ways to enhance efficiency and sustainability, ultrasonic sewing stands out as a key player in the future of textile production. Embracing this technology could lead to innovative designs, reduced costs, and improved product quality, ensuring its place in the evolving fabric of manufacturing.